Ceramic Forming Capabilites
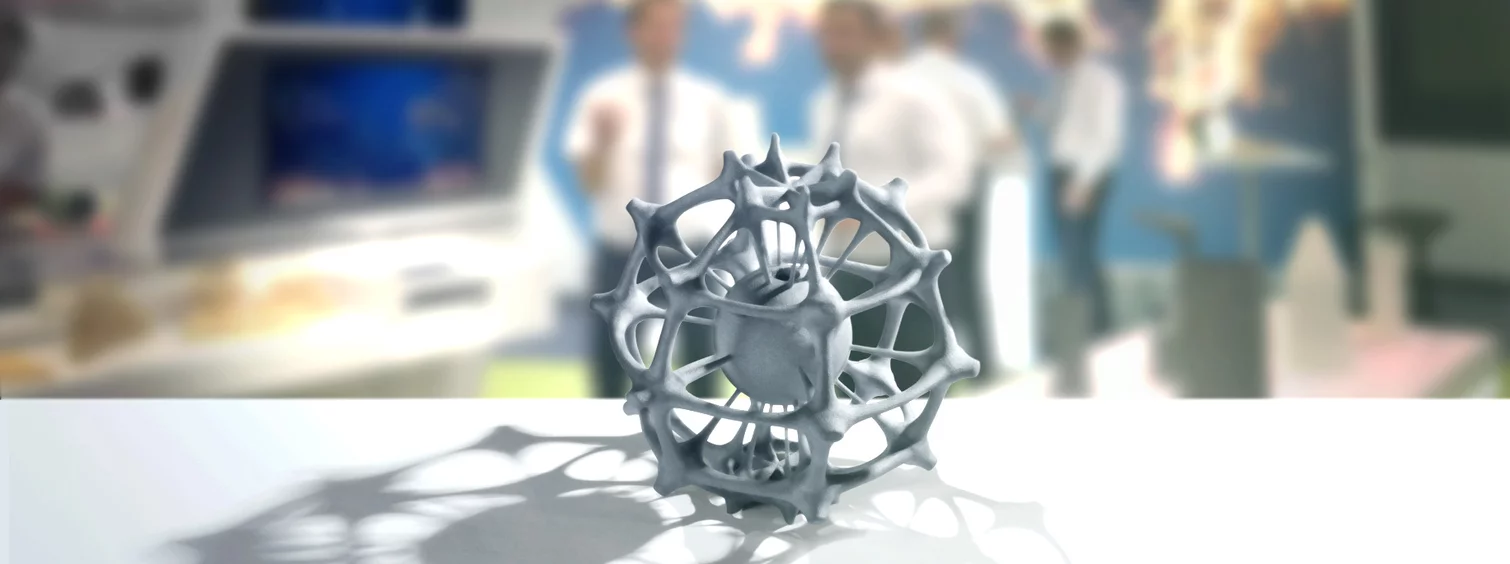
Economical Ceramic Shaping that meets Requirements
The selection of the appropriate ceramic molding process depends on the desired end properties, geometry, and size of the components to be manufactured. The number of pieces, raw material input, and process costs additionally determine which process is most economical.
Die Casting
Slip Casting
Dry Pressing
Isostatic pressing
Extrusion
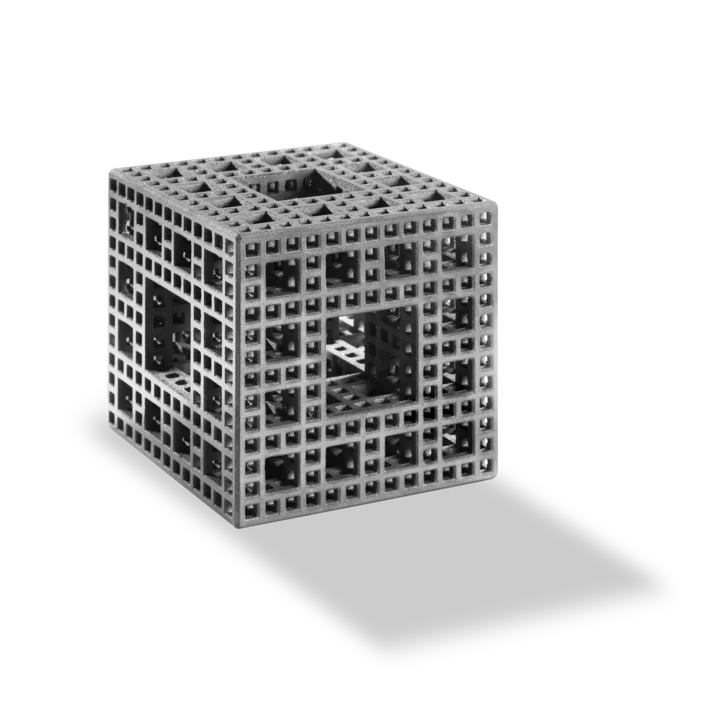
3D printing with IntrinSiC®
IntrinSiC®, the new 3D printing process from Schunk Technical Ceramics, is used to additively manufacture ceramic components in even more complex shapes, high quality, and numerous sizes. The new manufacturing process is particularly interesting for manufacturers who do not want to forego the usual high stiffness and strength of RB-SiC for large, complex components. IntrinSiC® offers the globally-unique possibility of producing 3D-printed RB-SiC consistent with material produced using conventional manufacturing processes. It is also characterized by very high uniformity in all three spatial directions. Components up to a size of 1.8 m x 1.0 m x 0.7 m can be realized. In addition, IntrinSiC® offers the opportunity for maximum topology optimization. IntrinSiC® offers customers from a wide range of industries completely new possibilities, for example in industrial precision and metrology or space applications.