Finite Element Simulation
In the classic development and design of ceramic components, prototypes must be designed and subjected to material tests before they are put into use. If these tests are negative, it is necessary to modify the design. This iterative process can be repetitive, extending time to market and increasing development costs. With the help of simulation, components can be virtually tested in their design state before the first prototype is produced, drastically reducing development times and costs. The use of the finite element method (FEM), a computer-aided calculation method for optimizing the design of the component, has proven its worth.
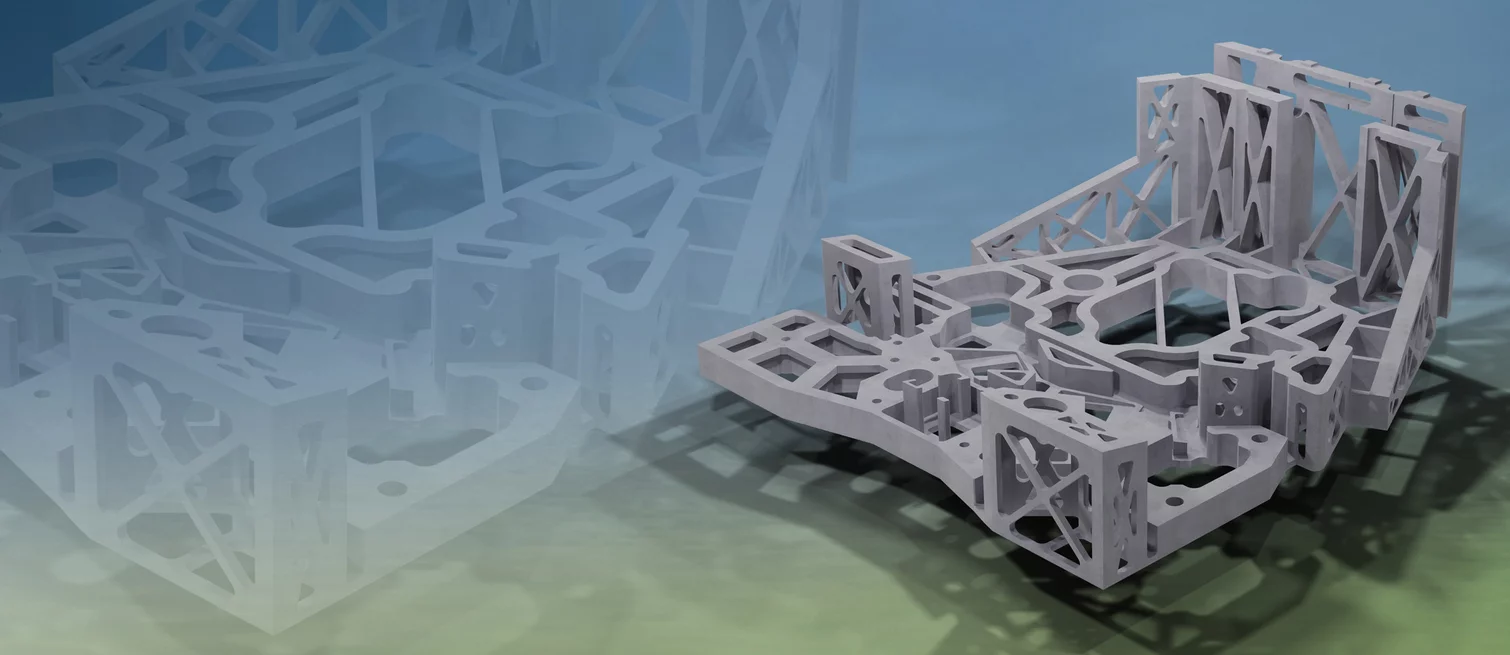
Simulation-based development of components made of technical ceramics
Maximum Possible Weight Reduction with Increased Component Strength
FEM analysis (including strength calculations) is used to decisively optimize components in terms of reliability and weight savings. For this purpose, a 3D model of the component with the ceramic material properties is created and subjected to virtual loads corresponding to the operating conditions. The identified overloads of the material can be taken into account in the design optimization. This significantly reduces the amount of physical testing of the components, as the mechanical or thermal performance of the product are thus improved even before the first use. Schunk Ceramics offers the execution and evaluation of the FEM calculation as an additional service.
Advantages of FEM simulation for product development
FEM simulations shorten development times and reduce the number of prototypes and thus also development costs. Special deformation analyses reveal weak points or even over-dimensioning. In combination with topology optimization, the material can be reduced at the points subject to little stress. The strength verification can thus contribute to material-efficient design.
FEM simulation service from Schunk Technical Ceramics
Not every company has its own FEM software. A lack of materials know-how and little experience with the finite element method - in interaction with the framework conditions of the shaping processes - can also lead to problems. As a long-standing manufacturer of components made of technical ceramics, Schunk Ceramics uses its great expertise and offers the FEM calculation as well as the evaluation of the results as an additional service. In this way, unnecessary prototype loops and many iteration steps can be avoided.