Light, precise, hard, durable – ceramics can simply do more
Mechanical Engineering. Meeting the Highest Requirements.
High-performance applications require high-performance materials. With the striving for lower weight, higher precision and durable load-bearing capacity, mechanical engineering is constantly pushing into new frontier areas. It's a good thing that our advanced ceramics are at home in precisely these areas.
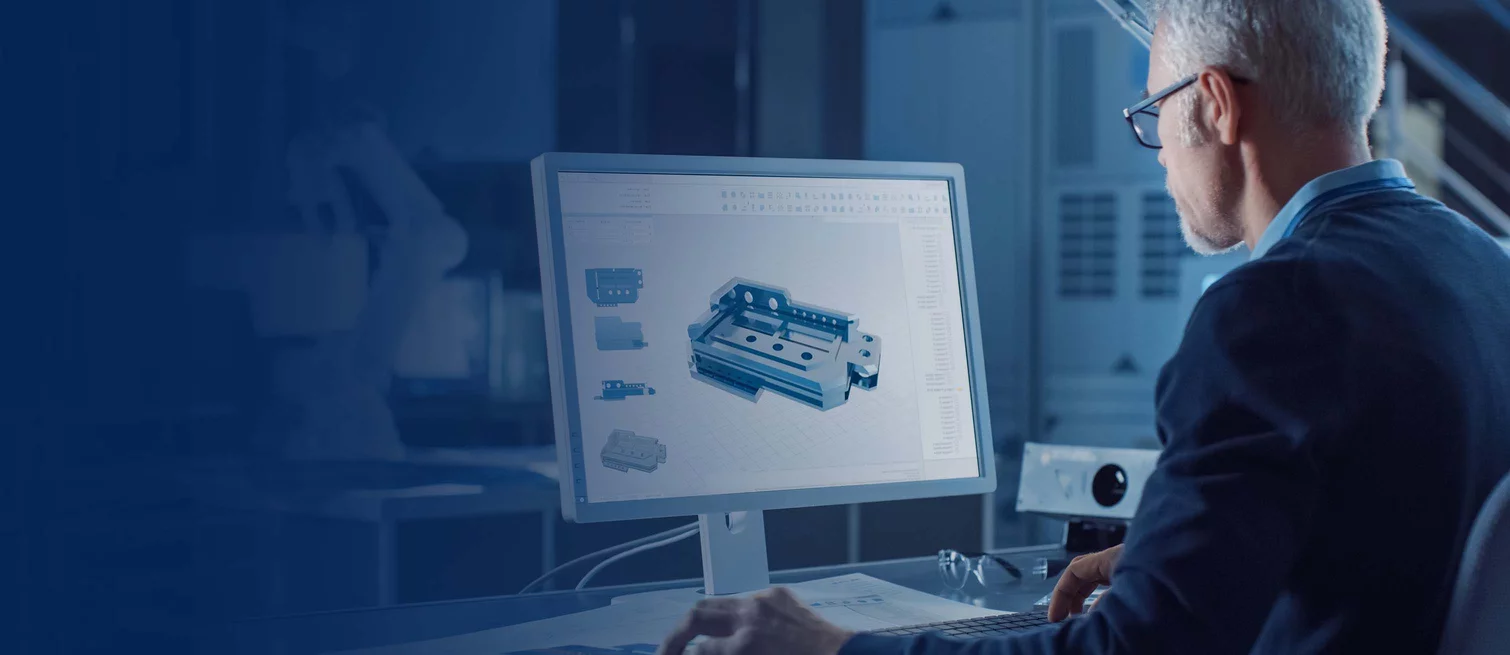
Challenges in the High Performance Industry
High-performance machines require high-performance materials. Whether in aerospace, metrology or semiconductor technology, the quest is for minimized weights, increased load-bearing capacity and enhanced precision. When measuring machines reach the limits of the measurement accuracies to be realized, space applications require minimum weight at maximum load, or semiconductor systems enter the realm of atomic size during processing, ceramics are increasingly the only possible alternative to realize structural elements of the systems or individual process components.
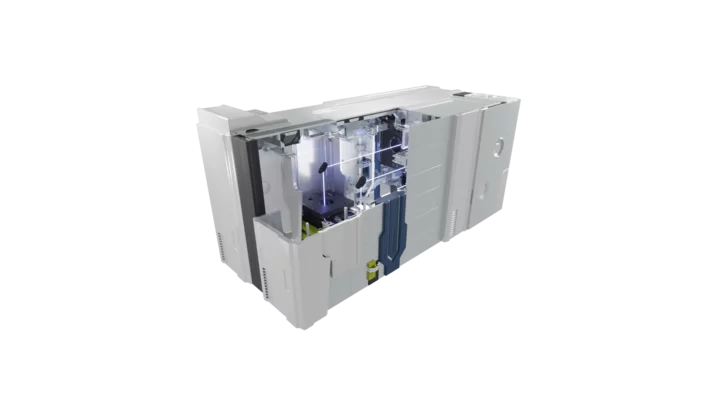
Mechanical Engineering
Huge power up to the μ-range
In frame components and wafer vacuum chucks for precision machines in the semiconductor industry, ceramics is a key material. It makes it possible to guarantee the position of the optics and sensors with the utmost precision so that the smallest nanometer structures can be achieved. Our patented manufacturing technology IntrinSiC® offers you advantages that are only available from Schunk: We are the only supplier who has been able to further develop the material in such a way that the required material properties are met and the component remains crack-free.
For solutions with the highest quality
With leading technologies in design, simulation, manufacturing and further processing, Schunk develops your components flexibly, tailor-made and quickly. Benefit from our more than 25 years of know-how and our strength as the market leader for reaction-bonded SiC.
3D-printing
Ceramic shaping process
Ceramic finishing
Finite Elemente Simulation (FEM)
Design and construction
Boundless freedom with 3D printing
Our patented IntrinSiC® manufacturing process combines the outstanding material properties of silicon infiltrated reaction bonded silicon carbide (RBSiC) with the process engineering advantages of 3D printing. Where shapes were once defined by manufacturing processes, today it's all down to your imagination. IntrinSiC® offers you design potential in new dimensions - even large and complex structures with undercuts and cavities can be produced in a single manufacturing step. The machine hours required for geometry milling in other processes are thus completely eliminated. With IntrinSiC® you can significantly reduce your carbon footprint, making it easier to achieve your sustainability goals. Compared with conventional approaches, you save around 25% Co2 - and if you take into account the reusability of excess powder, the figure is as high as 70%.
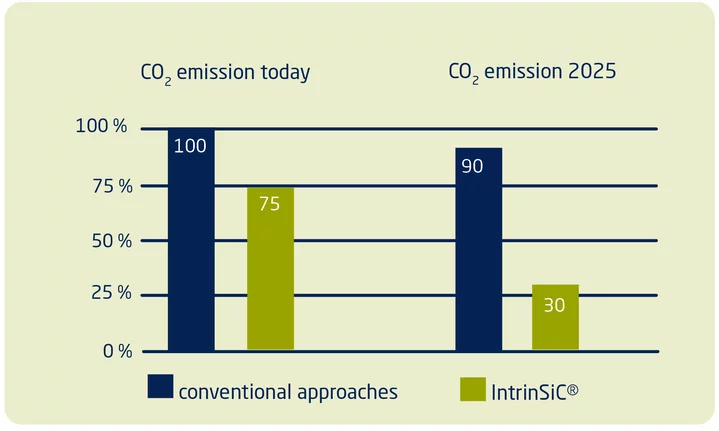
Material advantages of IntrinSiC®
- Very high stiffness, flexural strength and diamond-like hardness
- High thermal conductivity up to 200 W/mK
- Low thermal expansion
- Low density
- High dimensional accuracy
- High temperature resistance
- Excellent corrosion and oxidation resistance
- Component size 1.8mx1.0mx0.7m
- Bionic structures, topology optimized
- Strengths > 200 MPa and Weibull moduli >14
- CTE = 3.9 µ/K
- Reliability in small and large series
- Sustainable due to CO2 savings
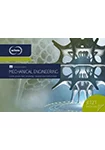