Introduction to ultrasonic metal welding
Using the Ultrasonic Metal Welding Technology, Materials Can Be Connected With Each Other
With ultrasonic welding, numerous materials can be joined to create cohesive bonds. The two largest material groups in this process are plastics and metals. In general, thermoplastic plastics are suitable for ultrasonic welding. Among metallic materials, aluminum and its alloys, as well as copper and its alloys, can be bonded efficiently and with high quality. Other metals, such as nickel, gold, and silver, can also be welded using the ultrasonic process, although these are usually special applications that require thorough analysis before selecting ultrasonic welding.
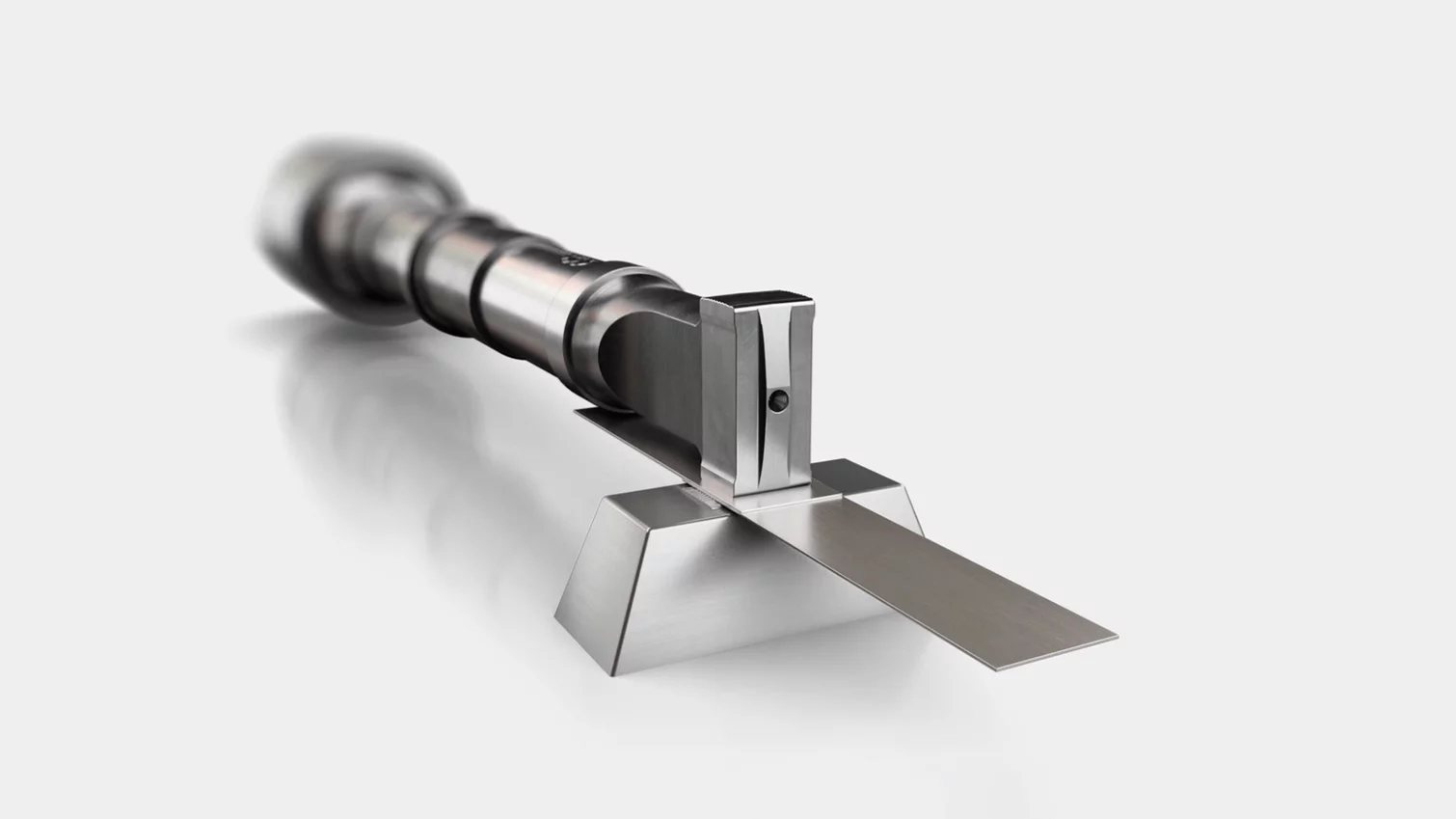
Discover. Ultrasonic Welding.
Ultrasonic welding is a pressure and friction welding technique
The oscillator system consists of three components: converter, booster and sonotrode. The converter transforms the high-frequency voltage into mechanical oscillation via piezo elements.
The booster is similar to an amplifier. The mechanical oscillation from the converter can either be amplified or reduced using a booster so that the amplitude of the sonotrode is optimized for its later use.
The sonotrode is the essential element; it transfers the high-frequency oscillation to the component being welded. For transferring the oscillation the sonotrode has a profile at the point of contact with the surface of the component which can be designed to be coarse or fine, depending on the welding task at hand.
Depending on the application, the oscillator systems are set to different frequencies. The most usual frequencies are 20 kHz 35 and 40 kHz. The rule here is that with increasing frequency the size of the oscillator system and the maximum transferrable welding power for joining components decreases.
Substance-to-substance bonding through metal welding
While in the case of plastic welding the parts being joined are brought into a liquid state, the bond is generated with both parts in a solid state during the metal-welding process. Although the melting point of the metals being bonded is never reached, high-strength metal bonds can be realized which are very similar to those achieved with conventional friction-welding processes. Ultrasonic metal welding results in a solid, homogenous and permanent metal bond far superior to surface adhesion or gluing. The two metallic materials permeate each other and are permanently and metallically bonded through short-distance diffusion within a fraction of a second.
Energy-Efficient Welding Techniques for Economically Significant Joining Tasks in Non-Ferrous Metals
Ultrasonic welding from Schunk Sonosystems offers a very energy-efficient and short welding process that maximizes productivity while minimizing heat input into the component. This preserves the material and ensures high reproducibility. Comprehensive process control provides reliable recognition of welding errors, resulting in consistently high-quality joints with outstanding electrical properties—ideal for demanding applications. Schunk Sonosystems also enables the welding of diverse material combinations, such as Cu & Al or glass-metal. The system meets the highest global safety standards and offers low investment, operating, and maintenance costs. Choose the ultrasonic technology from Schunk Sonosystems and experience the efficiency, reliability, and economy that your projects demand.
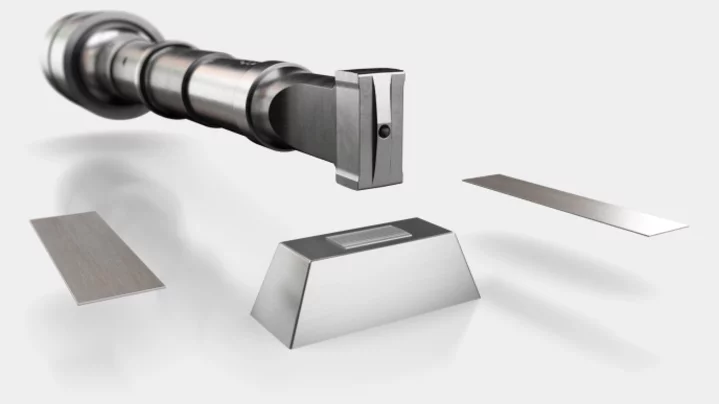
Spot Welding
The most common application for ultrasonic metal welding is so-called spot welding. Here the size of the welding spot can range from a few square millimeters to 100 square millimeters.
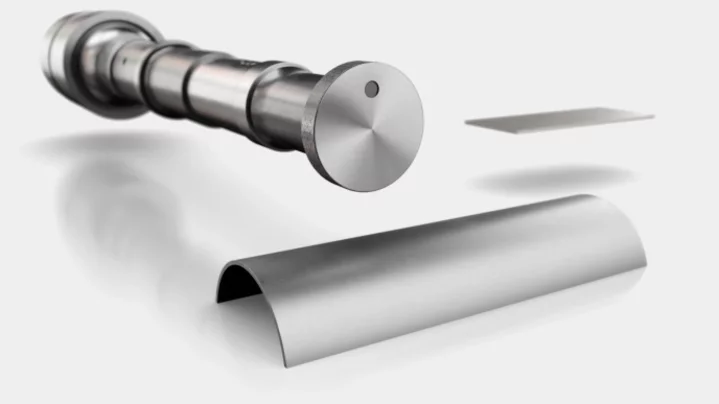
Roll Seam Welding
With roll seam welding a linear continuous metallic seam weld is produced. Typical applications include solar thermal power, photovoltaics and composite pipes production.
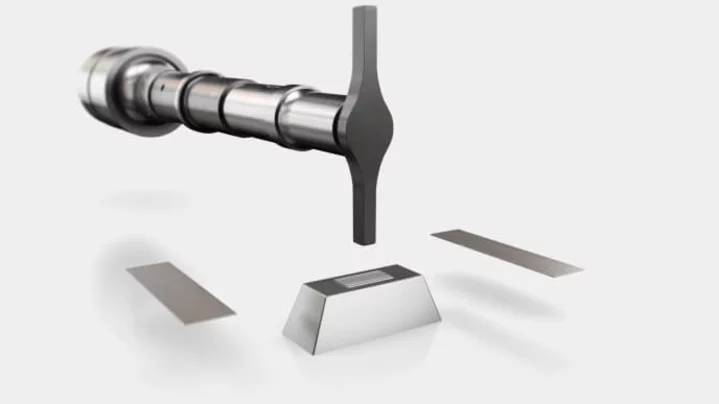
Bending Vibration
Bending horns are often used for welding spots which are difficult get at or reach. In contrast to a standard sonotrode, which produces longitudinal oscillation, the bending sonotrode is induced to generate flexural oscillation in the center by the vibrating oscillator system.
Advantages
Why You Need Ultrasonics from Schunk Sonosystems?
- Very energy-efficient and short welding process
- Very little heat input into the component
- High reproducibility
- Comprehensive process control with reliable recognition of welding errors
- Outstanding electrical properties of the joint
- Welding of diverse material combinations e.g. Cu & Al, glass - metal
- Highest global safety standards
- Low investment, operating and maintenance costs
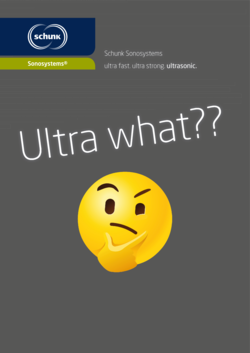
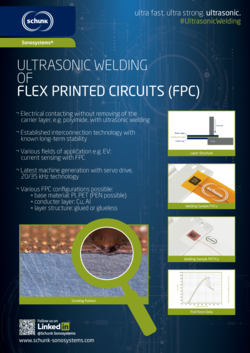
A handout about flex printed circuits (FPC).
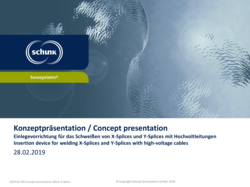
Insertion device for welding X-Splices and Y-Splices with high-voltage cables