Keramische Formgebungsverfahren
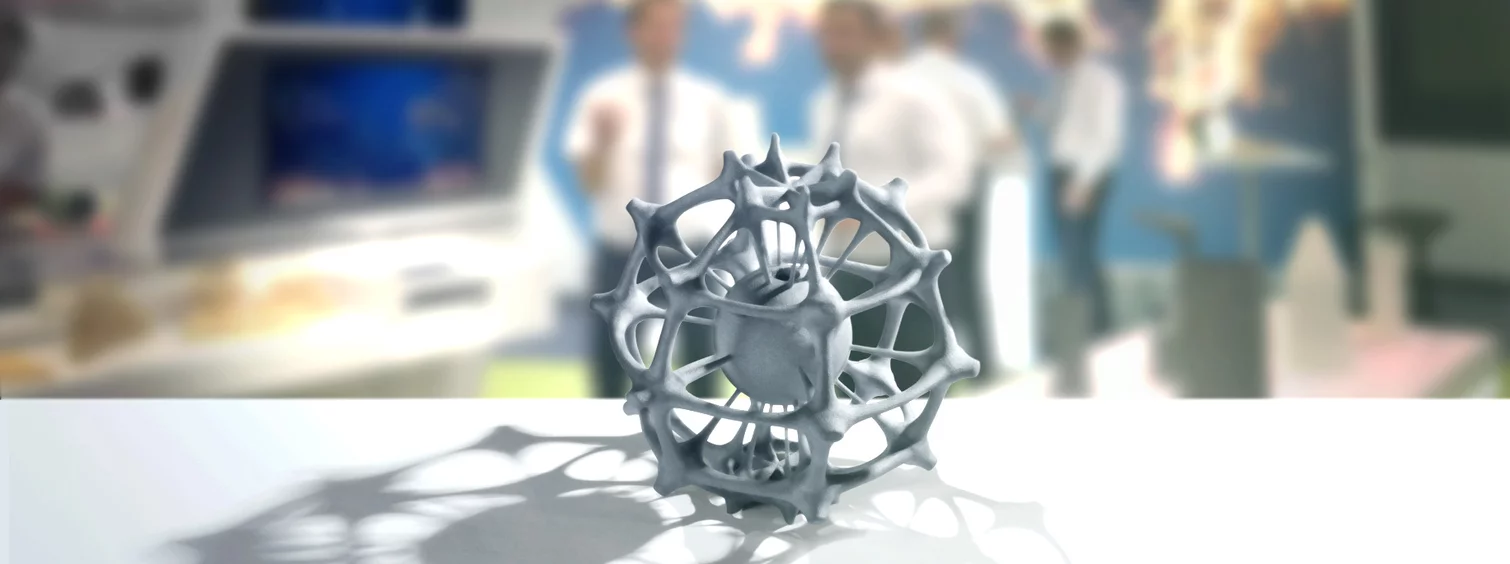
Wirtschaftliche und anforderungsgerechte keramische Formgebung
Die Auswahl des geeigneten keramischen Formgebungsverfahrens hängt von den gewünschten Endeigenschaften, der Geometrie und Größe der herzustellenden Bauteile ab. Stückzahl, Rohstoffeinsatz und Prozesskosten entscheiden zusätzlich, welches Verfahren am wirtschaftlichsten ist.
Druckguss
Schlickerguss
Trockenpressen
Isostatisches Pressen
Extrudieren
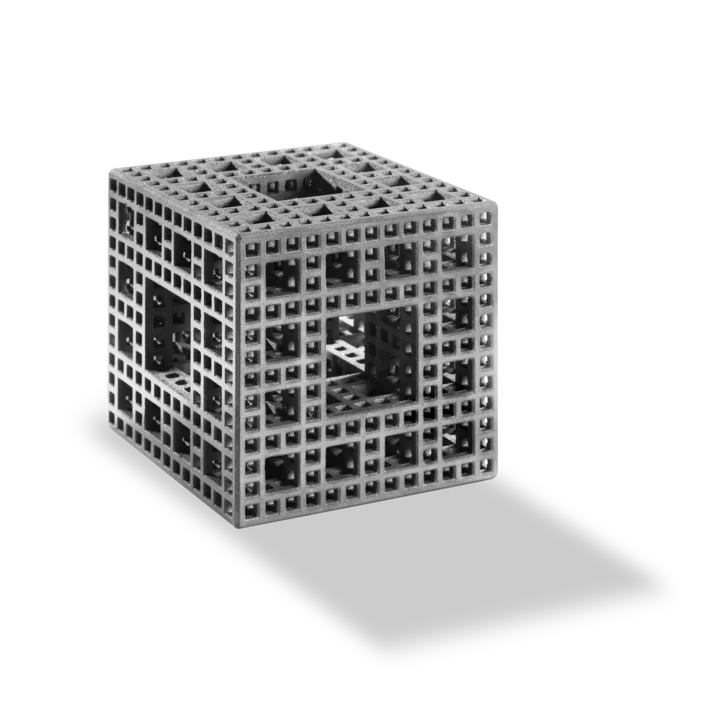
3D-Druck mit IntrinSiC®
Mit IntrinSiC®, dem neuartigen 3D-Druck-Verfahren von Schunk Technical Ceramics, werden keramische Bauteile in noch komplexeren Formen, hoher Qualität und zahlreichen Größen additiv gefertigt. Interessant ist das neue Fertigungsverfahren vor allem für Hersteller, die bei großen, komplexen Bauteilen nicht auf die gewohnt hohe Steifigkeit und Festigkeit des RBSiC verzichten wollen. IntrinSiC® bietet die weltweit einzigartige Möglichkeit, 3D-gedrucktes RBSiC auf dem Werkstoffniveau konventioneller Fertigungsverfahren zu erzeugen. Es zeichnet sich zudem durch eine sehr hohe Gleichmäßigkeit in alle drei Raumrichtungen aus. Bauteile bis zu einer Größe von 1,8 m x 1,0 m x 0,7 m sind realisierbar. Zudem eröffnet IntrinSiC® die Aussicht, bei der Topologieoptimierung das maximale Potenzial zu erschließen. Durch IntrinSiC® erhalten Kunden aus den unterschiedlichsten Branchen völlig neue Möglichkeiten, zum Beispiel in der industriellen Präzisions- und Messtechnik oder Spaceapplikationen.