The solution for oil quenching
Advantages
Special properties of our Durafox® oxide fiber composites:
- Significantly longer service life due to resistance to oxidation and corrosion
- High damage tolerance (ductile fracture behavior)
- Good thermomechanical properties
- Resistance to thermal shock and thermal cycling
- Distortion-free under thermocyclic stress enables quality improvement
- Low thermal conductivity
- Electrical insulator
- Lightweight construction (thin wall thicknesses can be realized)
- Metal-like, sheet-like designs possible
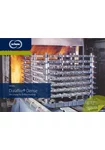
Brochure: Durafire® Dense
Add
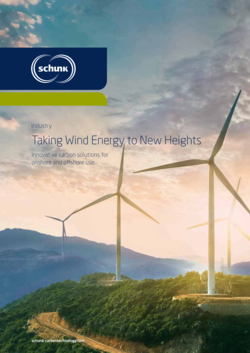
Brochure: Wind Energy
Innovative Carbon Solutions for Onshore and Offshore Use
Add
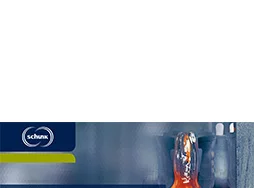
Brochure: Glass Handling
Schunk Industry: Leading the Way in Glass Handling
Add
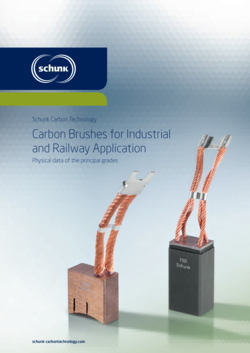
Physical Data: Carbon Brushes
for industrial and railway applications
Add
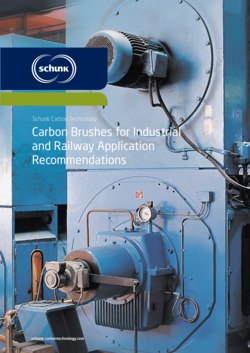
Recommendations: Carbon Brushes
for industrial and railway applications
Add
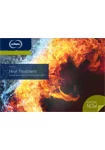
Brochure: Heat Treatment
Innovative Solutions for Thermal Applications
Add
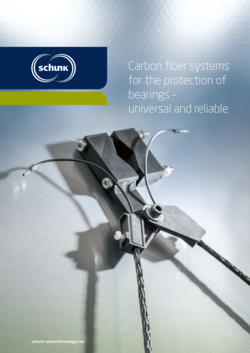
Brochure: Shaft Grounding
Carbon Fiber Systems for the Protection of Bearings - Universal & Reliable
Add
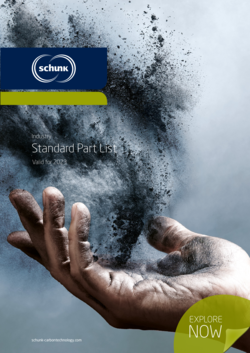
Standard Part List
Standard parts list in the field of high temperature applications
Add
Downloads
8 Files online