Effizienz, Reichweite und autonome Ladelösungen im Fokus
Dass Elektrofahrzeuge zu teuer sind, zu lange zum Laden brauchen, eine zu geringe Reichweite haben oder zum Laden immer ein Kabel angefasst werden muss, sind Argumente, die immer noch viele Kunden vom Kauf eines Elektroautos abhalten. Und auch im industriellen Bereich stellt die Forderungen nach umweltfreundlicherer Mobilität Unternehmen vor Herausforderungen. Damit Elektromobilität zum Beispiel für Logistikunternehmen eine wirtschaftlich interessante Alternative wird, braucht es Lösungen, die nicht nur schnelles, zuverlässiges Laden und hohe Reichweiten sicherstellen, sondern sich auch auf platzsparend im Depot integrieren lassen. Zum Glück geht die Entwicklung von Ladesystemen für Elektrofahrzeuge rasant voran. Mittlerweile umfasst die Bandbreite nicht nur manuell zu bedienende Ladesysteme, sondern auch autonome Lösungen.
Lesen Sie hier, welche Ladesysteme für welche Fahrzeugarten das meiste Potenzial bieten und wie eine Unterboden-Ladelösung das effiziente und platzsparende Laden von PKW und E-Trucks ermöglicht.
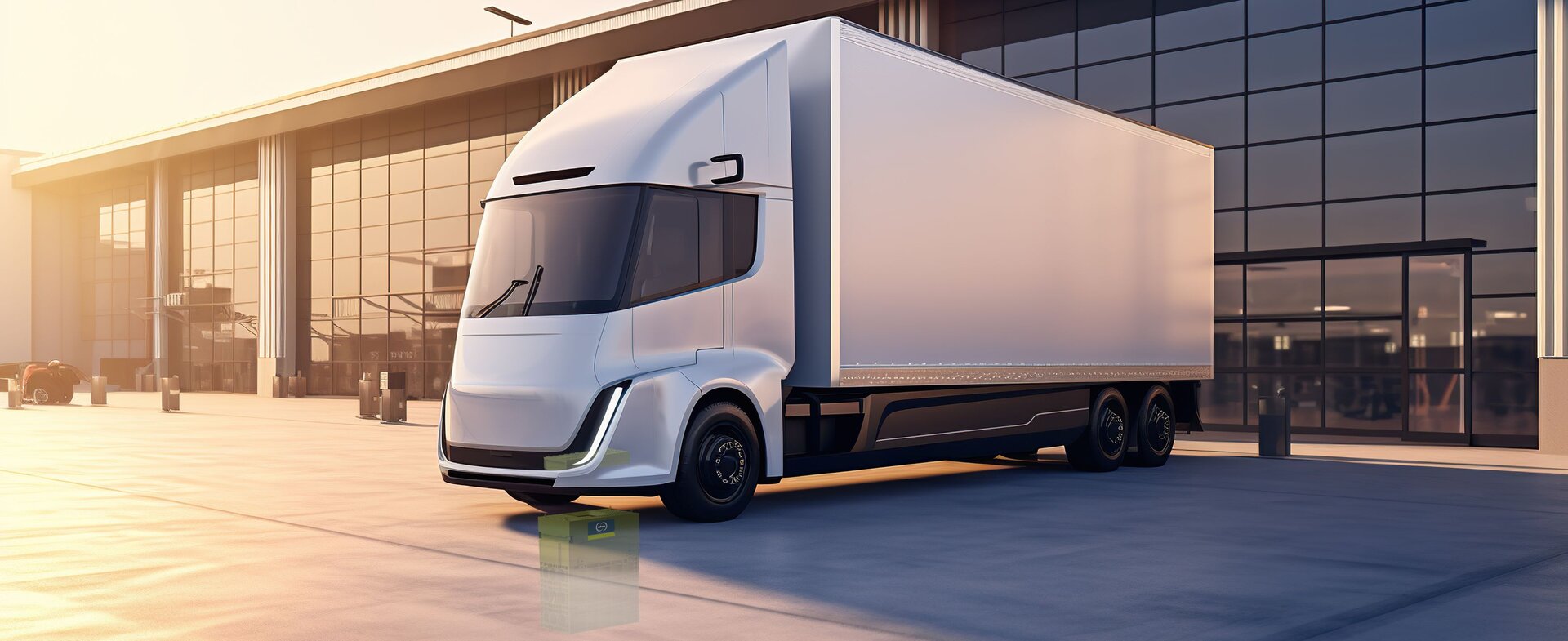
Überblick über Ladelösungen für Elektrofahrzeuge
Mittlerweile gibt es eine Vielzahl an Ladesystemen, die auf die Anforderungen unterschiedlicher Fahrzeugtypen vom PKW über Elektrobusse bis hin zu Industrie- und Nutzfahrzeugen zugeschnitten sind. Die breite Auswahl reicht von der einfachen Haushaltssteckdose über leistungsstarke Schnellladestationen bis hin zu innovativen, automatisierten Lösungen wie dem Underbody Charging.
Hier eine Übersicht der derzeitigen Ladelösungen:
Bezeichnung |
Technologie |
Ladeleistung |
Anwendung |
Beschreibung |
Potenzial |
Haushaltssteckdose (Schuko) |
Konduktive Steckerlösung |
bis zu 2,3 kW |
PKW |
weit verbreitet, aber langsame Ladezeiten, geeignet als Notlösung |
niedrig |
Wallbox |
Konduktive Steckerlösung |
3,7 bis 22 kW |
PKW |
Ideal für den täglichen Gebrauch zu Hause, sicherer und effizienter als normale Steckdosen. |
hoch |
Öffentliche Ladestation |
Konduktive Steckerlösung |
11 kW bis 50 kW |
PKW |
Entscheidend für die breite Akzeptanz von Elektrofahrzeugen, verfügbar an vielen Standorten.
|
hoch |
Schnellladestationen (DC-Schnellladen) |
Konduktive Steckerlösung |
50 kW bis über 350 kW |
PKW |
Wichtig für Langstreckenfahrten, relativ kurze Ladezeiten.
|
sehr hoch |
Induktives Laden, drahtloses Laden |
Induktive Lösung |
3,6 kW bis 11 kW (PKW)
50 kW bis 150 kW (E-Trucks)
|
PKW, E-Trucks |
Bequem und benutzerfreundlich, aber noch technologische Herausforderungen und höhere Kosten. |
mittel bis hoch |
Mobile Ladelösungen (zum Mitnehmen) |
Konduktive Steckerlösung |
bis zu 3,7 KW (PKW), bis zu 50 kW (E-Trucks) |
PKW und E-Trucks |
Flexibel und nützlich für Notfälle oder abgelegene Orte, weniger effizient als fest installierte Lösungen. |
mittel |
High-Power Charging Stations (HPC) |
Konduktive Steckerlösung |
150 kW bis 500 kW |
PKW, leichte Nutzfahrzeuge |
Entscheidend für die schnelle Aufladung von E-Trucks, besonders auf Langstrecken. |
sehr hoch |
Phantograph Charging |
Konduktive Kontaktlösung |
150 kW bis 1 MW |
E-Trucks, E-Busse, elektrische Industriefahrzeuge |
Ultra-schnelle und automatische Aufladung, ideal für Flotten und den öffentlichen Nahverkehr.
|
hoch |
Depot Charging |
Konduktive Stecker- oder Pantographenlösung |
50 kW bis 150 kW |
E-Trucks, E-Busse |
Effizient für das Laden über Nacht oder während längerer Leerlaufzeiten in Logistikzentren.
|
hoch |
Megawatt Charging System (MCS)
|
Konduktive Steckerlösung |
über 1 MW |
E-Trucks und Busse |
Extrem hohe Ladeleistungen, noch in der Entwicklung, enormes Potenzial für den Schwerlasttransport. |
sehr hoch |
Underbody Charging |
Konduktive Lösung |
1 MW |
PKW und E-Trucks |
Automatisches Aufladen durch im Boden eingelassene Ladevorrichtung, besonders benutzerfreundlich und platzsparend, geeignet für städtische und private Anwendungen sowie Logistikzentren. |
hoch |
Der Underbody Charger als Ladesystem für Elektroautos und E-Trucks
Der Underbody Charger ist eine effiziente Ladelösung, die sowohl für PKWs als auch für LKWs geeignet ist. Das System bietet eine hochleistungsfähige und platzsparende Möglichkeit, Elektrofahrzeuge effizient zu laden, indem die Ladeinfrastruktur im Boden integriert wird. Der automatische Ladevorgang kann selbst bei vollständig entleerten Batterien auf wenige Minuten verkürzt und einfach in den alltäglichen Gebrauch der Fahrzeuge integriert werden.
Die Funktionsweise des Underbody Chargers
Der Underbody Charger funktioniert, indem das Fahrzeug über eine im Boden eingelassene Ladevorrichtung fährt. Das Ladesystem fährt aus, verbindet sich mit der im Fahrzeugboden verbauten Andockvorrichtung, sobald das Fahrzeug korrekt positioniert ist, und startet automatisch den Ladevorgang. Mit einer Ladeleistung von bis zu 1 MW kann das Fahrzeug während normaler Be- und Entladevorgänge vollständig aufgeladen werden, ohne dass zusätzliche Ladepausen erforderlich sind. Nach dem Ladevorgang zieht sich das Ladesystem wieder in den Boden zurück, sodass der Platz weiterhin nutzbar bleibt.
So profitieren Nutzer von dem automatisierten Unterboden-Ladesystem
- Platzsparend: Die Integration in den Boden bedeutet, dass kein zusätzlicher Platz für Ladestationen benötigt wird. Ein klarer Vorteil in beengten städtischen Gebieten und Logistikzentren.
- Hohe Ladeleistung: Mit bis zu 1 MW Ladeleistung ermöglicht der Underbody Charger schnelle Ladezyklen, wodurch die Effizienz und Einsatzbereitschaft der Fahrzeuge maximiert wird.
- Automatisierung: Kabel anfassen unnötig! Der Ladevorgang erfolgt vollautomatisch, ohne dass der Fahrer das Fahrzeug verlassen oder manuell Kabel anschließen muss. Dies spart Zeit und reduziert den Arbeitsaufwand.
- Sicherheit: Da keine direkte Handhabung von Hochspannungskabeln erforderlich ist, wird das Risiko von Unfällen und elektrischen Gefahren minimiert.
- Flexibilität: Geeignet sowohl für PKWs als auch für LKWs, bietet dieses System eine vielseitige Ladelösung für verschiedene Fahrzeugtypen und Anwendungsbereiche.
In diesen Anwendungen punktet der Underbody Charger
Der Underbody Charger spielt seine Stärken überall da aus, wo platzsparende Lösungen und schnelles Laden gefragt ist. Das automatisierte Ladesystem ist daher vor allem für den Einsatz in urbanen und industrielle Umgebungen prädestiniert.
Zum Beispiel in:
- Städtischen Logistikzentren: Ideal für den Einsatz in dicht besiedelten urbanen Gebieten, wo Platz eine begrenzte Ressource ist.
- Lagerhäusern und Depots: Ermöglicht die effiziente Nutzung der Standzeiten während des Be- und Entladens der Fahrzeuge.
- Öffentlichen Ladestationen: Die Unterboden-Lösung kann auch an öffentlichen Ladestationen für die Langstreckenlogistik installiert werden
Wie das Ladesystem für Elektrofahrzeuge genau funktioniert, erfahren Sie in diesem Video.
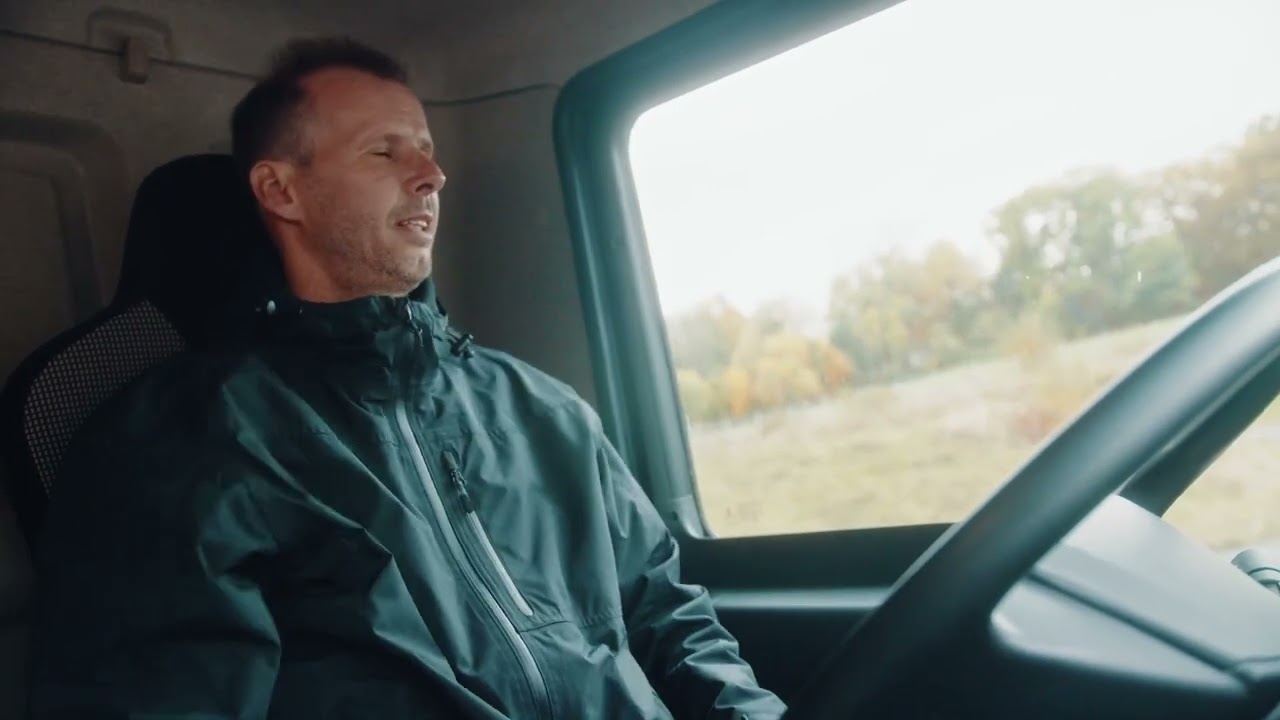
Vielversprechende Entwicklung für attraktive E-Mobilität
Auch wenn lange Ladezeiten, begrenzte Reichweiten und das Handling mit Hochspannungskabeln immer noch Herausforderungen darstellen: Mittlerweile gibt es vielversprechende Entwicklungen für unterschiedlichste Anforderungen, die das Potenzial haben, diese Hürden zu überwinden. Automatisierte Ladesysteme wie der Underbody Charger maximieren die Effizienz durch hohe Ladeleistungen und platzsparende Installation im Boden. Sie bieten eine sichere, automatische Lademöglichkeit, was besonders in städtischen Logistikzentren und privaten Garagen von Vorteil ist. Insgesamt tragen diese Entwicklungen dazu bei, die Elektromobilität wirtschaftlich und attraktiv zu machen.
FAQ Unterbody Charger als Ladesystem für E-Trucks und E-Auto
Wie lange dauert es, bis ein Elektrofahrzeug mit dem Ladesystem Underbody Charger aufgeladen ist?
Im Vergleich zu Steckerlösungen ermöglicht das autonome Laden mit dem Underbody Charger eine Zeitersparnis von 75 Prozent. Die Ladeleistung von 1 Megawatt verkürzt die Ladezeit von Elektroautos von 45 Minuten auf 10 Minuten. Bei E-Trucks beträgt die Ladezeit 30 Minuten anstatt 2 Stunden.
Welchen Einfluss hat das Schnellladen auf die Lebensdauer der Batterien?
Der Underbody Charger ist für das Schnellladen von modernen Batterien konzipiert, die mit einer Rate von 3, 4 oder 5C aufgeladen werden können. Bei diesem Batteriestandard hat das Schnellladen keinerlei negativen Einfluss auf die Fahrzeugbatterien.
Wie groß ist das Gewicht der fahrzeugseitigen Hardware?
Bei unserem Serienprodukt wird das Gewicht bei zwei bis drei Kilogramm liegen.
Wo kann ich den Underbody Charger im Einsatz sehen?
Der Underbody Charger ist in einer Vielzahl von Projekten im Einsatz. Zum Beispiel
- als Ladelösung für Elektroautos für einen Logistikbetreiber in Hannover,
- als Ladelösung für E-LKW eines Logistikzentrums in Berlin und
- auf dem Testgelände für E-LKW des Fraunhofer Instituts in Dresden.
Interessiert an weiteren Informationen? Hier finden Sie alle relevanten Broschüre und Dokumente zum Thema.
Jetzt herunterladen